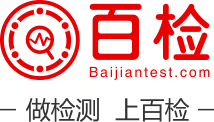
2017年1月,在新年气息正浓的底特律,戴姆勒公司为全球车市奉上了一份别样的“年礼”——在连续刷新销量纪录的第6个年头,梅赛德斯-奔驰以2016年全年首超200万辆的业绩,提前4年实现重返豪华品牌全球销量**的目标。而北京奔驰历经11年的时间,也实现了后来居上,在2016年实现全年销量31.7万辆,同比增长超过30%,跃居国内豪华车合资品牌次席。
在中国已然成为梅赛德斯-奔驰乘用车*大单一市场的环境下,2016年,31.7万辆的销量数据,刷新了北京奔驰成立至今的销量记录,占奔驰在华销售业绩的近七成。在这一年里,北京奔驰完成了**百万台国产梅赛德斯-奔驰发动机与整车的下线,以及全新梅赛德斯-奔驰E级车下线,就此,北京奔驰实现了“同一车型、两种不同轴距”产品的同步投产,在全面满足了中国消费者日益多元化的驾乘需求的同时,开启了中国智造与智能驾驶的崭新篇章。可以说,北京奔驰为奔驰品牌重返豪华车全球销量**起到了重要作用。
当我们回溯其发展历程,不难看出,北京奔驰在用基础建设、以软实力驱动的助推力以及产销一体化运作,为如今的逆势而起与高速突破打下了坚实的基础。
夯实基础建设 打造硬实力
精准布局
2013年2月1日,随着北汽集团、北京汽车与戴姆勒公司合作协议*终达成一致,股东双方围绕资本、制造、产品开发、技术等层面的全产业链合作全面展开,北京汽车股份有限公司与戴姆勒大中华区投资有限公司合资组建北京梅赛德斯-奔驰销售服务有限公司。
以合为先、平台发力的战略,使北京奔驰走上了高速前行的发展轨道。基于平台化,北京奔驰的思路从“车型的被动导入”转向了“快速响应市场需求”,呈现出步步为营的变化。
平台为先
在随后短短5年的时间里,戴姆勒全球产能*大的总装车间、戴姆勒公司海外**家质量中心、戴姆勒公司**海外的梅赛德斯-奔驰汽发动机制造工厂、戴姆勒合资公司里*大的研发中心、戴姆勒全球*先进的前驱车工厂等诸多项目纷纷落户北京奔驰。成立后的十年时间内,北京奔驰建立起全球面积*大、综合性*强的梅赛德斯-奔驰乘用车生产制造基地,并成为戴姆勒全球**同时拥有前驱车、后驱车和动力系统三大平台的合资企业。
有如预期,基于平台化的优势,北京奔驰在其后的产品导入游刃有余。2010年,北京奔驰推出了梅赛德斯-奔驰长轴距E级轿车,产品结构调整的序幕正式拉开。此后的一年,北京奔驰又抓住市场契机,及时引入了GLK SUV,创造了项目当年实施、当年投产的奇迹。同年,北京奔驰投放C级轿车中期改款车型,产品市场竞争力进一步增强。
从2014年7月,全新长轴距C级车上市,刷新了中级豪华轿车本地化生产的标准,其后,北京奔驰相继推出了**基于MFA平台的GLA紧凑型豪华SUV、以及基于MRA平台的标准轴距C级车和新GLC豪华中型SUV,吹响了北京奔驰冲击中国豪华汽车**位置的号角。
2016年6月16日,全新梅赛德斯-奔驰长轴距E级车下线,拉开了中国智造与智能驾驶的崭新篇章,5个月后,标准轴距E级车下线,标志着北京奔驰完成了对产品序列的拓展和更新,全面覆盖中**轿车、行政级轿车、紧凑型SUV和中型SUV四大豪华车主流细分市场。
品质引航
产品之上,北京奔驰在不断强化自身导入、消化和吸收梅赛德斯-奔驰**工艺的能力的基础上,逐步构建起**未来的智能化制造体系,并依托这一体系,打造了完善的质量管理系统,并建成了戴姆勒公司海外**家质量中心。
借由高科技的生产智能控制系统,北京奔驰从发动机机加工,到冲压、装焊、涂装和总装四大工艺中所使用的数千台制造机器人,均具备了识别、沟通和对工作指令进行应答的能力。在全面遵循戴姆勒的质量反馈环管理的同时,智能化制造系统与一系列****的智能化检测系统、监控系统的**整合,实现了对生产制造过程的全面数据化监控和记录。在此基础上,核心数据与戴姆勒全球数据库同步并实时共享,真正意义上实现了产品品质的可追溯与全球标准化,从根本上确保驶出北京奔驰的每一辆新车都完全符合梅赛德斯-奔驰的全球统一标准。
现阶段,北京奔驰发动机3C件机加工自动化率高达95%,装焊工艺在85%以上、喷漆70%以上;柔性化生产能力的稳步增强,使三种不同轴距车型的混线生产成为现实;在此基础上订单式生产的实现,使北京奔驰的所有产品都可根据客户需求实现高品质的定制化生产,为用户提供多种多样的个性化选装包;与此同时,在生产过程中,物料自动配送平台“购物车”(AGV+shopping cart)会把依照用客户订单需求分类整理好的成套配件,准时送到指定工位,员工无需走动即可完成精准装配,在有效降低劳动强度的同时,*大提升了生产效率与装配精度。